Zap Out Motor Problems: How to Detect Electric Motor Defects
In the world of machinery and equipment maintenance, ensuring motor reliability is crucial for smooth operations. Electric motors play a fundamental role in driving various industrial processes, making it essential to detect any defects early on to prevent costly downtime. By proactively identifying issues within electric motors, maintenance professionals can avoid unexpected failures and keep operations running efficiently.
Detecting electric motor defects requires a combination of knowledge, observation, and the use of diagnostic tools. Understanding common signs of motor problems, such as unusual noises, vibrations, or temperature variations, can help technicians pinpoint potential issues before they escalate. Additionally, utilizing technologies like thermal imaging and vibration analysis can provide valuable insights into the internal health of electric motors, enabling timely interventions to prevent catastrophic failures.
Common Motor Defects
One common motor defect is overheating, which can occur due to issues with lubrication or excessive loading. Overheating can lead to insulation breakdown and shorten the motor's lifespan, affecting its reliability.
Another common defect is bearing failure, often caused by lack of proper lubrication or contamination. Bearings play a crucial role in the motor's operation, and failure can result in increased friction, noise, and even complete motor breakdown.
Electrical faults, such as short circuits or ground faults, are also common motor defects. These faults can cause the motor to malfunction, resulting in erratic behavior and potential safety hazards. Regular inspection and maintenance are key to detecting and addressing these issues promptly.
Diagnostic Tools
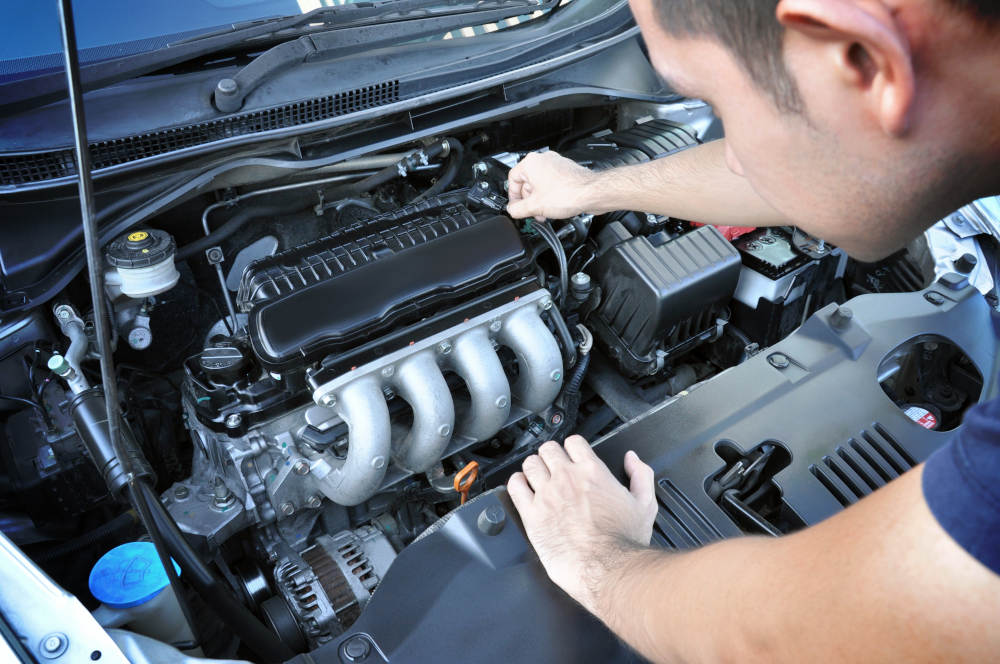
When it comes to ensuring motor reliability, using the right diagnostic tools is crucial. One of the most common tools for detecting electric motor defects is the multimeter. This device can measure voltage, current, and resistance, providing valuable insights into the health of the motor.
Another essential tool is the insulation tester. By checking the insulation resistance of the motor windings, this tool can help identify any potential insulation breakdown issues, which are common causes of motor failure. Regularly testing insulation resistance can catch defects early and prevent costly downtime.
Thermal imaging cameras are also valuable diagnostic tools for electric motors. These cameras can detect overheating components in the motor, indicating potential issues that need attention. By regularly monitoring motor temperatures with thermal imaging, maintenance teams can proactively address defects before they escalate.
Preventive Maintenance
Regular maintenance is key to ensuring motor reliability. In order to prevent potential defects, it is essential to conduct routine inspections. This involves checking for any unusual noises, vibrations, or excessive heat coming from the motor.
Furthermore, keeping the motor well-lubricated is crucial for its optimal performance. Lack of proper lubrication can lead to increased friction, which in turn can cause overheating and premature wear on motor components. By regularly monitoring and replenishing lubricants, you can extend the lifespan of the motor.
Lastly, implementing a scheduled maintenance program is highly recommended. This program can include tasks such as cleaning the motor, checking electrical connections, and conducting thermal imaging tests. By staying proactive with maintenance efforts, you can minimize the risk of unexpected breakdowns and ensure the long-term reliability of the motor.